What happens when you order a set of wheels from us. (310) 936-8521
- kesajian
- Mar 14, 2024
- 1 min read
Updated: May 20, 2024
1. The design is established.
2. The sizes are established, i.e. diameters and widths.
3. Third is the finishes, there’s a lot to choose from. There's a fully polished, brushed barrel with polished or powder coated center face, brushed center with polished barrel. You can create a lot of combinations as well.
4. The next part of the order is fitment. We have a chart specifically for measurements to get the most wheel under your car without rubbing.
5. After all of the above is established we get a 50% deposit to start the build which takes approximately 6 weeks give or take.
6.Here’s what happens on the back end of starting your order. Based on the wheel design we discuss which billet forging will be the best to accommodate the bolt pattern and disc brake clearance. We order the forgings which are manufactured here in California. The machine work
takes a couple weeks due to orders in process. After the center face is machined it is taken to polish and or powder coat. Sometimes the wheel after it is assembled is sent to the powder coater.
Assembly is done after we receive the center face from the polish or powder coater. We order the rim shells which are also made in the US, Indiana. We heat the rim shells, put them on a heavy block leveled table with the backspace plates. Once the wheel cools we check the run out
for being true. Then it goes to weld, then we true it on the lathe. The valve stem hole is drilled and the wheel is detailed and boxed.
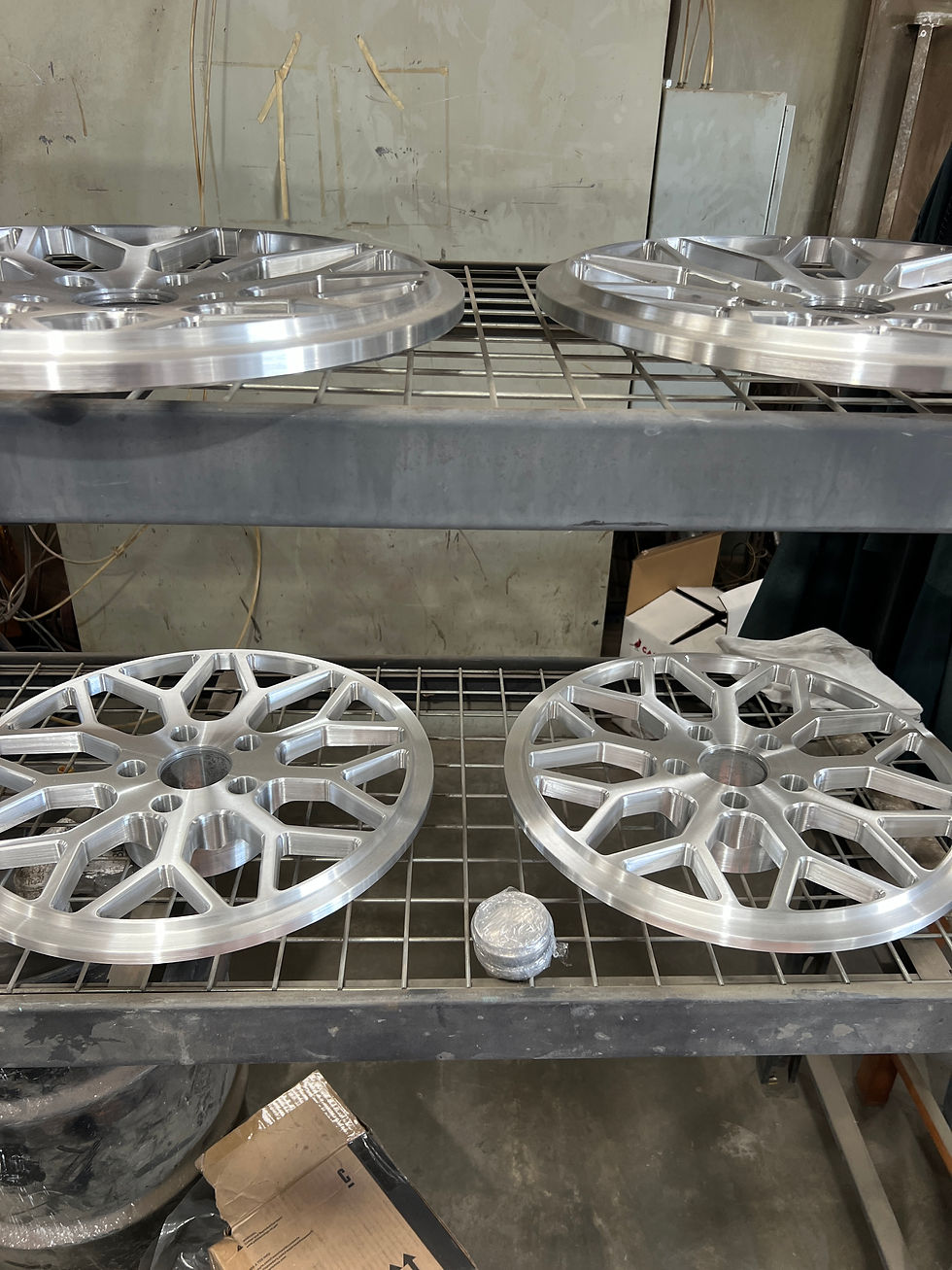
Comentarios